In today’s shipping and distribution industries, “picking” is big business. Warehouses filling orders for companies like Amazon employ thousands of pickers to hustle back and forth between the shelves, collecting items to be boxed up and sent off to customers. It can be a grueling job, and even smaller, less-demanding businesses can struggle with the logistics of filling orders quickly and correctly. SmartPick, from Belgian engineer Dirk Matheeussen, hopes to make the process simpler.
SmartPick is, essentially, augmented reality software. It runs in the Android OS and is designed for Vuzix M100 smart glasses — like Google Glass, but optimized for industry. The M100 has larger batteries and can clip onto the safety goggles many warehouse workers already have to wear.
The glasses recognize printed codes attached to the pallet or shelf space of each item in the warehouse. As a picker looks around, the SmartPick software overlays graphics on top of those codes in the picker’s field of view, telling her how many of each item to collect — and even where to go to find the next item in the order.
It’s a streamlined system meant to improve on existing order filling techniques. Older systems rely on handheld devices, which can be clumsy and tie up the hands a picker needs to move boxes and grab product. Some recent systems went hands-free by using automated voice guidance, which relies on the picker to remember the instructions or use voice recognition to repeat them — kind of like talking to one of those infuriating telephone customer service computers. Others use a system of lights to indicate where the picker’s target item lives, and small screens attached to the shelves to provide further information. The drawback there is both the cost of the hardware, and the difficulty of rearranging the warehouse once it’s been installed.
SmartPick is designed to be hands-free and intuitive, and to reduce the overhead costs of infrastructure and equipment. The application integrates with existing warehouse management software that tracks orders and supplies layout information about the warehouse. So all a distributor needs to get started using SmartPick is the Vuzix glasses and a printer.
“Eventually it will replace the headset of a voice picking system or the screen of a light picking system,” Matheeussen tells Postscapes.
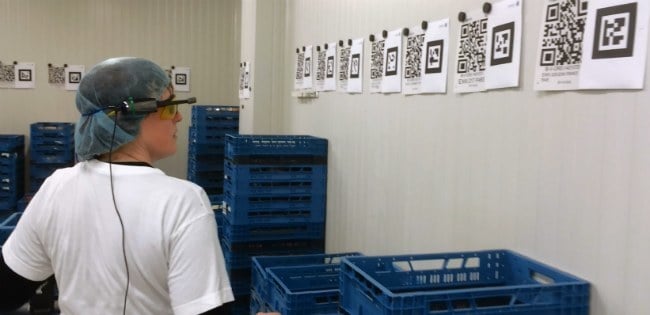
It’s already in use in a handful of bakery warehouses in Belgium, where workers distribute dozens of types of bread to hundreds of stores. So far, Matheeussen says, his system has reduced errors by 60 percent and boosted productivity by 25 percent.
Matheeussen says the future of SmartPick lies in becoming an OEM partner for vendors of warehouse management systems, who will be able to offer a complete package including smart glasses running the SmartPick app along with warehouse management software. The first such partnership is with Distrib AR, from Netherlands-based firm Pcdata.
Learn more at SmartPick.be.